Quality
: the degree of excellence of something, often a high degree of it
What it all means
We've all heard the word and most of us have entire departments dedicated to it. But why?
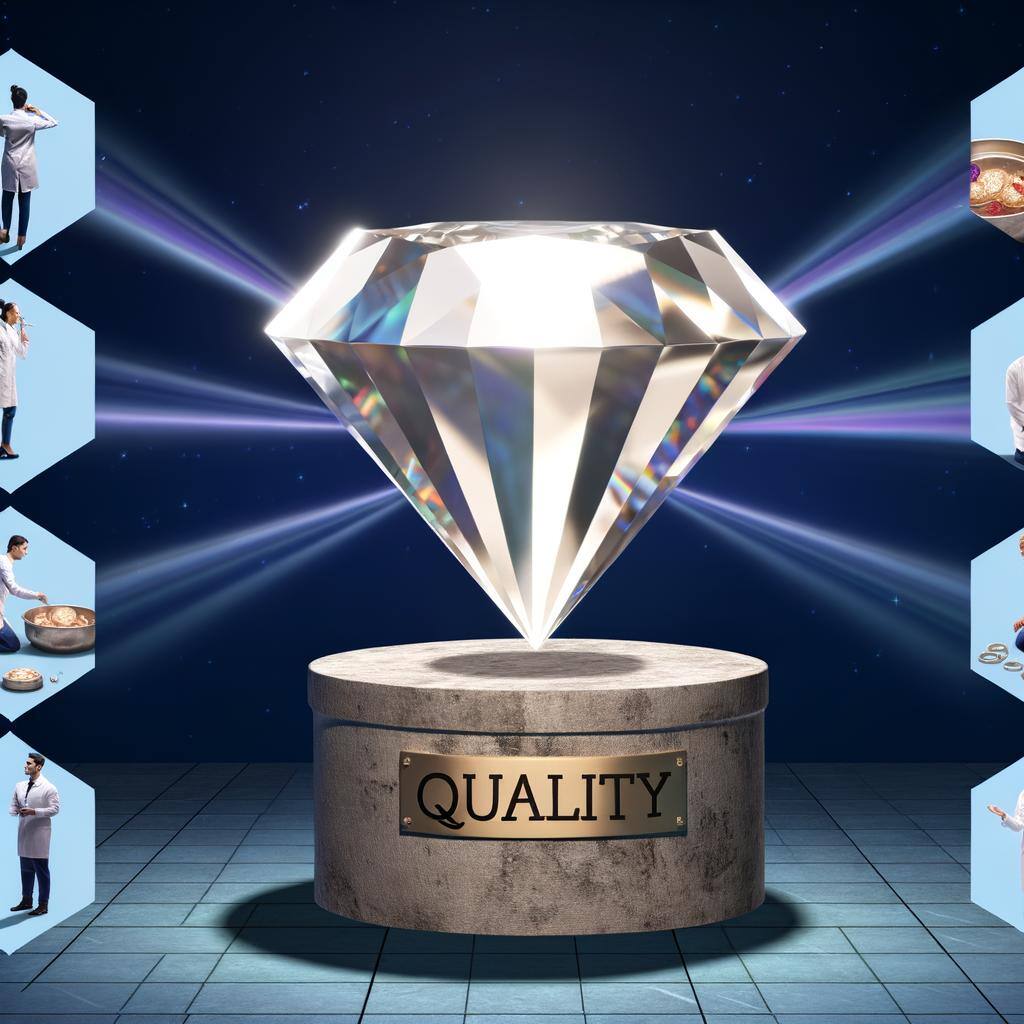
How important is it?
Quality, specifically a high level of quality, is something we all strive to bring to our products every day. That's what keeps the customers coming back, right?
Well, yes, it's true that customers will likely not return if our product quality is below their expectations or declining over time.
Therefore, since our customers are the lifeblood of our business, shouldn't we spend a lot more time thinking about, focused on, and making improvements in our quality?!
It's a goal and a process.
So we've established that we need to be more concerned about quality in our organization. But now what? What are the key points to consider?
One: quality, specifically high quality is our ultimate goal.
Two: high quality products, regardless of the designer's skill or the assembler's focus, will not just magically appear day after day.
Three: the solution is not difficult, it just takes planning, persistence, and unwavering support from you, the company executive.
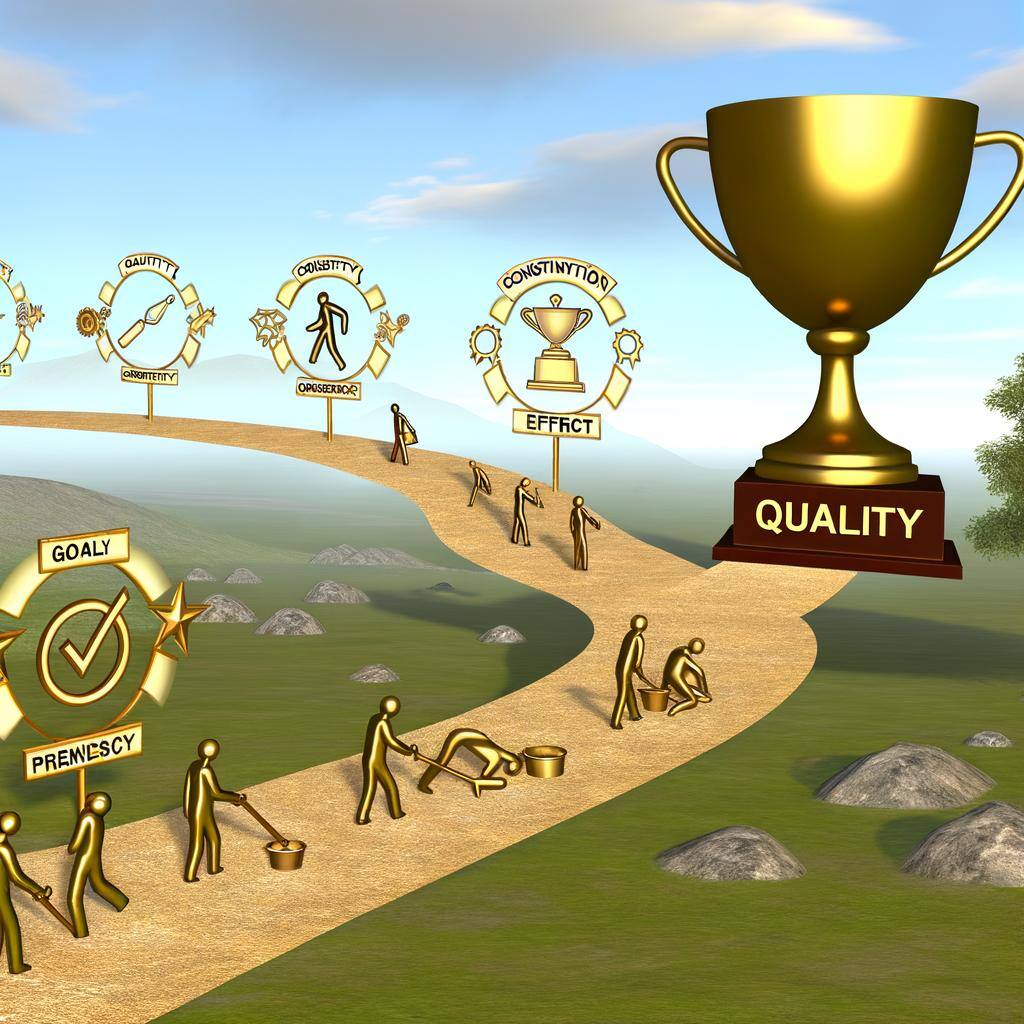
Keys to Success
As mentioned above, a process must be followed to achieve the goal.
-
Clearly defined procedures
Consistency is key.
If you were baking a cake and the recipe only said:
- some butter
- a little flour
- as much sugar as you likemost of the time, the results would not be as you expected - or possibly even resemble a cake!
There must be clearly defined instructions (procedures) to ensure that you get the same high quality result each time.
-
Quality starts at the beginning
To ensure that your product leaves the building with the highest quality possible, the focus needs to start much earlier.
All the way back to the beginning, when the product is still on the drawing board. Your designers and engineers need to keep quality in mind as they design - as they choose materials, decide on features and tolerances, and plan their testing. We can help them with that.
Your suppliers, and how you choose to communicate with them, will also impact your final product quality. There's a process. We can help.
And finally, your shop floor. Where the parts come together, the product is built and packaged, and shipped to your customer. There needs to be a defined process. We can help.
-
Be consistent
Just like the cake recipe mentioned above, the key to ensuring you always ship the highest quality product possible is to be consistent.
Define what you're going to do, do it, and then confirm that you did it and how well.
Wash - rinse - repeat. It's really that simple.
-
PDCA
PLAN - DO - CHECK - ACT
: is an iterative design and management method used in business for the control and continual improvement of processes and products.
This is the 'wash, rinse, repeat' mantra that should be ingrained in all areas of your business.
It has been around for decades, but few implement and practice it as well as the Japanese. Having worked in a Japanese environment for more than a decade, I've seen it work. I've seen the benefit of making this part of your business. I can help you do the same.
-
Everyone is included
We've all heard the old saying, "it takes a village to raise a child". Well, it takes everyone in your company to fully ensure that your product goes out as expected (quality, cost, and delivery) every time.
As an executive in your company, it's your responsibility to make sure that the village (your company and employees) take the best possible care of the child (your products).Don't leave anyone out. Everyone can, and must, contribute to your corporate success.
-
Live and learn
Like the PDCA process enforces, your particular experience with quality has likely been one of "live and learn".
We all go through that, but it's crazy for all of us to suffer through the mistakes that others have already solved.Lean on us to help educate you and your team. Benefit from the mistakes we have made in the past. Benefit from The Method.
Are you ready to improve your organization's quality?
We will review your current procedures and processes to help you identify the gaps and then bring the right experience and tools to level up the quality within your processes and your products.